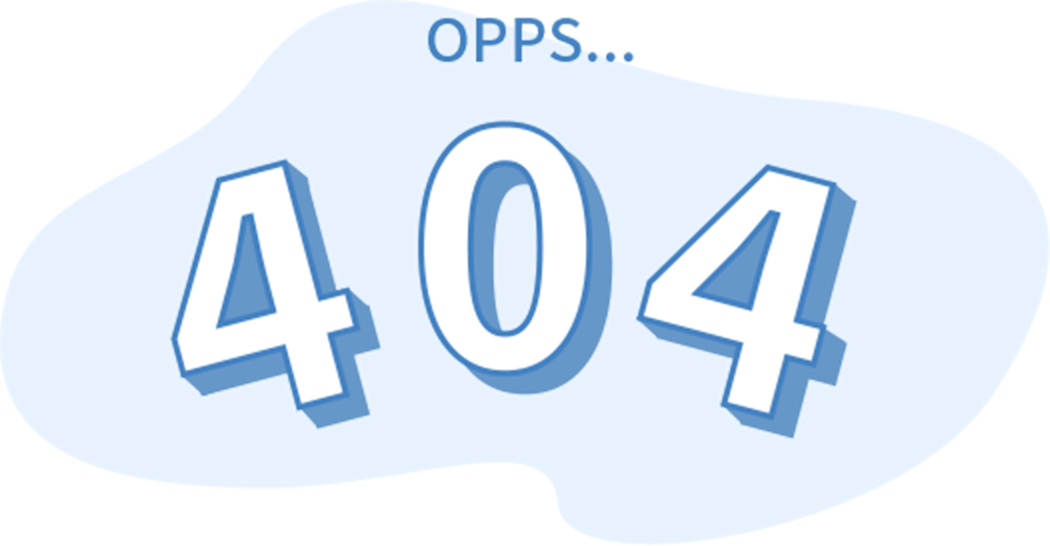
Fuya Denim - Professional Wholesale Denim Fabric And Jeans Fabric Supplier In China
Fuya Denim - Professional Wholesale Denim Fabric And Jeans Fabric Supplier In China
CONTACT US
SALES DIRECTOR : Bill Xu
Phone/whatsapp:
+86 18038870959
Email: [email protected]
SALES CENTER ADDRESS:
Block E , NO1-2, New Cowboy Town, Da li Yanbu pingdi, Nanhai District, Foshan City
Copyright © 2021 Guangzhou Feng Gu Textile Co., Ltd.